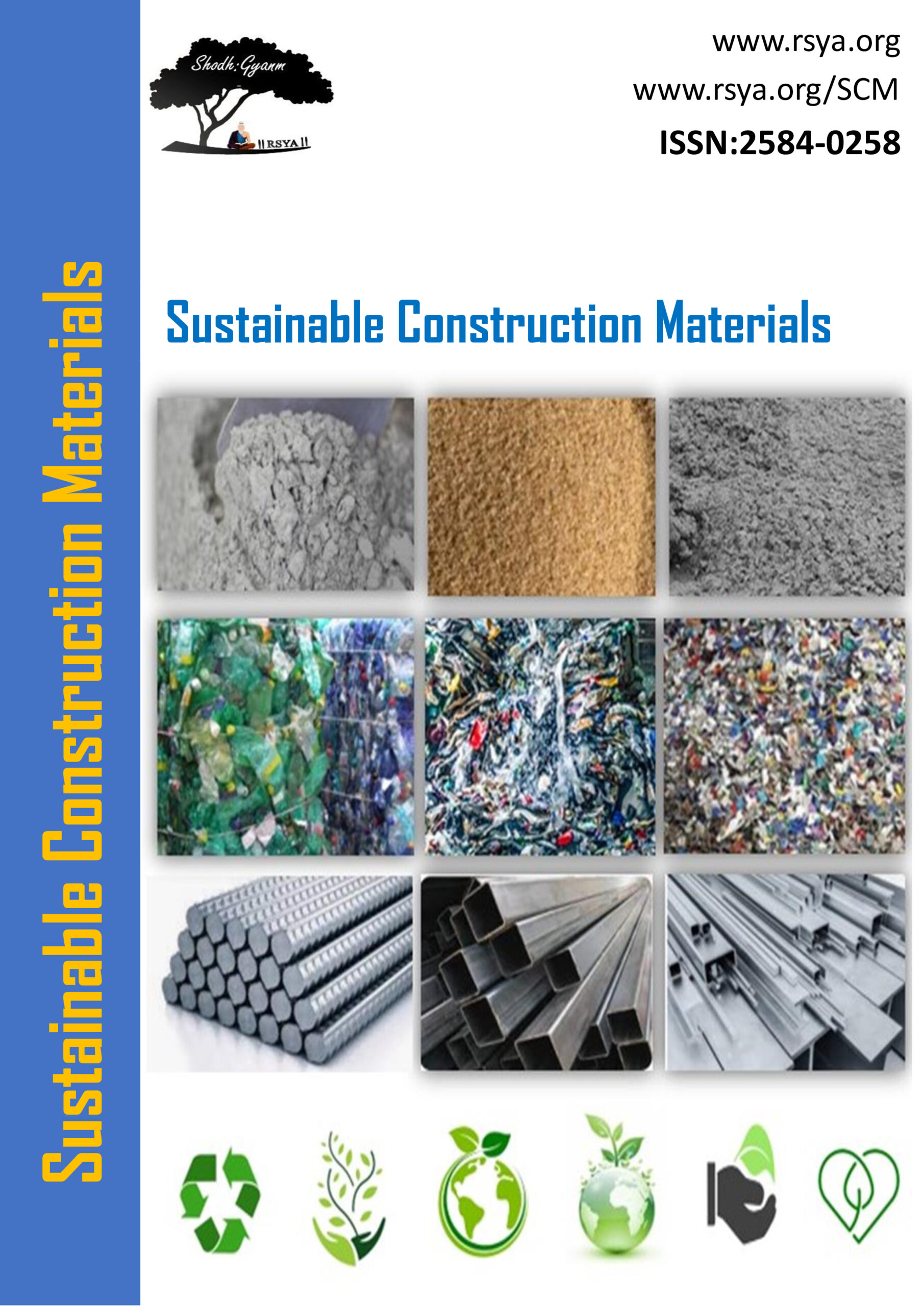
Civil Engineering, Construction Engineering & Management, Material Engineering
ISSN: 2584-0258 Open Access, Double Blind Review
Abstract and Indexing: Road, Google Scholar
Under Review: Scopus(Applied), UGC-Care(Applied), WoS (Applied)
Research Article
Shivam Dubey*, Yasir Khan
Vol 3 Issue 1, Pages 11 - 17
Abstract- In A long-term option for turning industrial waste into geopolymer composites is alkali activation of ground-granulated blast-furnace slag (GGBS) and calcined clay. The development of calcined clay-based geopolymer mortar and ground granulated blast furnace slag (GGBS) is the goal of this work. Alkaline activator is used to activate the aluminium silicates that make up GGBS and calcined clay. The alkaline activator is created using solutions of 8 M sodium hydroxide. Geopolymer consistency, setting time, and compressive strength were examined at ages 3, 7, and 28 days in relation to mixture proportioning and curing conditions. Process parameters such as the proportion of calcined clay, GGBS, fines content, and alkaline activator solution content were all studied. The experimental findings demonstrated that increasing the proportion of calcined clay in geopolymer mortar improved consistency and setting time. The highest compressive strength is reached when GGBS was employed 100 percent of the time in the mortar mix, and as the proportion of calcined clay replaced by GGBS in the mortar mix increased, the compressive strength decreased.